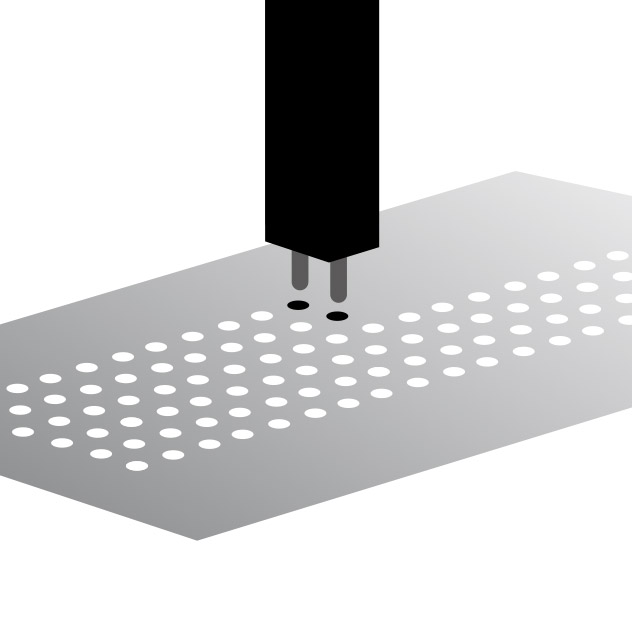
Sectional presses
Punching on a sectional press is the classical perforation technique. The process in carried out section by section and, with modern CNC control, individual perforation arrays can be made up. With quick and economical use of tools already on hand, the sectional press is ideally suited to handle thicker sheets and larger perforations.
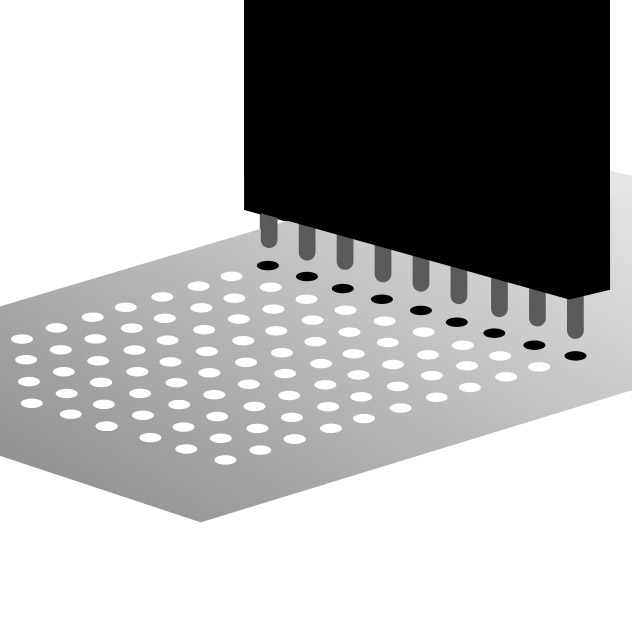
All across press
All across presses are designed to perforate the whole width of a sheet or coil in stroke. One or several rows of punches perforate the material at high speed while the material is fed step by step through the machine. All across presses are used primarily for production from coils and are most economical for the production of larger quantities of thin materials and smaller holes.
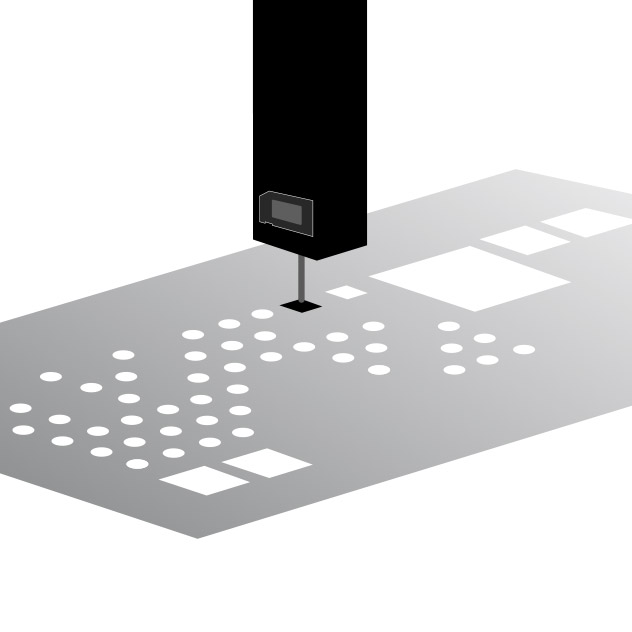
Turret punch press
A broad variety of hole shapes can be cut in a single pass using our turret punch and nibbling machine. Hole shapes and patterns which deviate from the norm can also easily be made up. In addition, exact contouring is possible using the CAD-CAM module or a DXF-file which you provide.
![[Translate to Englisch:] Plasmabrennanlage](/fileadmin/user_upload/004.jpg)
Thermal cutting machine
To complete our performance spectrum we offer the possibility of creating perforated sheets by thermal cutting. Depending on the material and its thickness, holes and contoures can be produced at laser quality. Thermal cutting or without cutting oxygen are available on demand.
![[Translate to Englisch:] Stanz-Lasermaschine](/fileadmin/_processed_/0/3/csm_fahl_stanz_laser_e8ef8a4782.png)
Laser punching machine
Cutting with a laser has mostly advantages: a high component accuracy in the thin sheet thickness range enables the laser to cut very small holes, narrow webs, and acute-angled geometries. The production of complex component contours is possible as well as right-angled cutting edges. The laser punching machine has very good automation capabilities, an extremely low heat input; as a result no deformation of the workpieces can be expected.
A very small kerf width (0,2 mm to 0,4 mm) and high cutting speed in the thin sheet metal sector (to approximately 4 mm) are futher advantages.
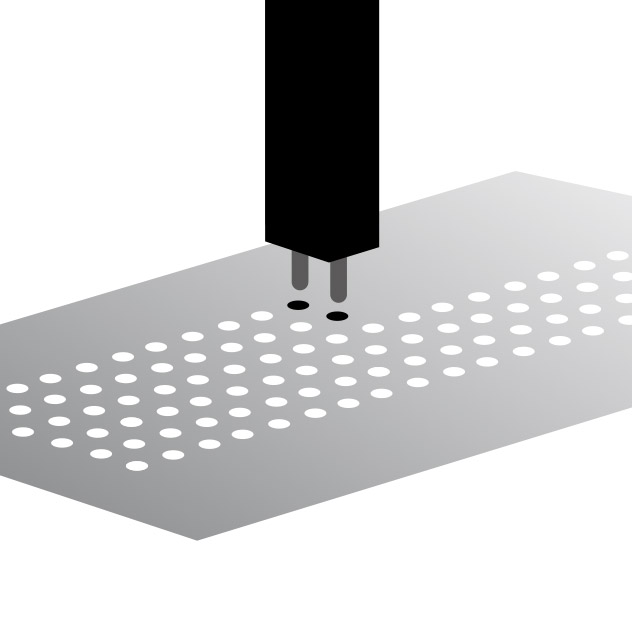
Sectional presses
Punching on a sectional press is the classical perforation technique. The process in carried out section by section and, with modern CNC control, individual perforation arrays can be made up. With quick and economical use of tools already on hand, the sectional press is ideally suited to handle thicker sheets and larger perforations.
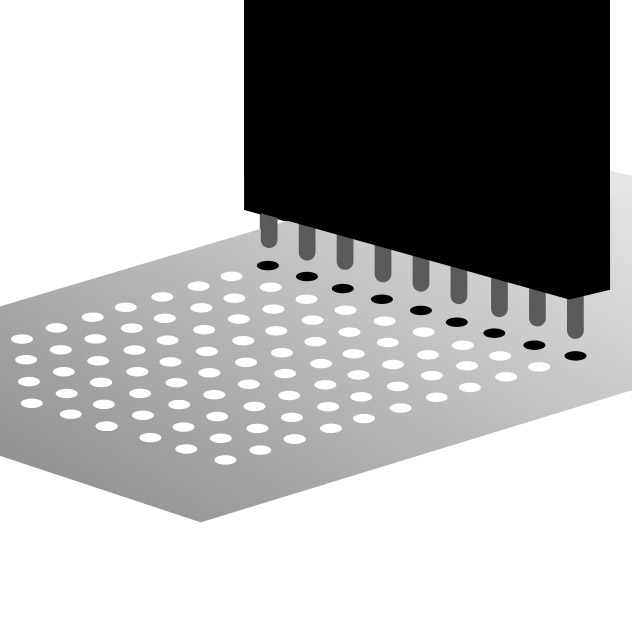
All across press
All across presses are designed to perforate the whole width of a sheet or coil in stroke. One or several rows of punches perforate the material at high speed while the material is fed step by step through the machine. All across presses are used primarily for production from coils and are most economical for the production of larger quantities of thin materials and smaller holes.
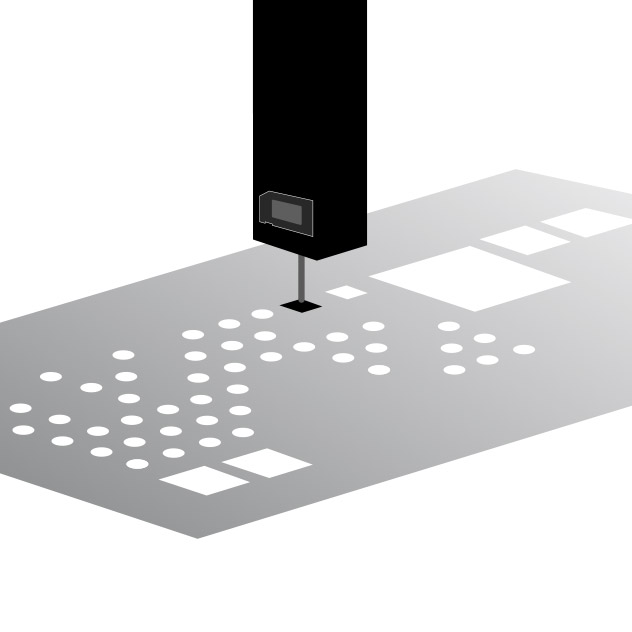
Turret punch press
A broad variety of hole shapes can be cut in a single pass using our turret punch and nibbling machine. Hole shapes and patterns which deviate from the norm can also easily be made up. In addition, exact contouring is possible using the CAD-CAM module or a DXF-file which you provide.
![[Translate to Englisch:] Plasmabrennanlage](/fileadmin/user_upload/004.jpg)
Thermal cutting machine
To complete our performance spectrum we offer the possibility of creating perforated sheets by thermal cutting. Depending on the material and its thickness, holes and contoures can be produced at laser quality. Thermal cutting or without cutting oxygen are available on demand.
![[Translate to Englisch:] Stanz-Lasermaschine](/fileadmin/_processed_/0/3/csm_fahl_stanz_laser_e8ef8a4782.png)
Laser punching machine
Cutting with a laser has mostly advantages: a high component accuracy in the thin sheet thickness range enables the laser to cut very small holes, narrow webs, and acute-angled geometries. The production of complex component contours is possible as well as right-angled cutting edges. The laser punching machine has very good automation capabilities, an extremely low heat input; as a result no deformation of the workpieces can be expected.
A very small kerf width (0,2 mm to 0,4 mm) and high cutting speed in the thin sheet metal sector (to approximately 4 mm) are futher advantages.
Small format (KF) 1000 x 2000 mm
Medium format (MF) 1250 x 2500 mm
Large format (GF) 1500 x 3000 mm
Super format (SF) 2000 x 4000 mm
Of course we deliver cuttings
Raw material/material
Materials which are normally processed: Perforated sheets, coils and custom size sheets can be manufactured from all suitable materials such as steel (blank steel, pre galv. steel, highly wear-resistant alloys), stainless steel, non-ferrous metals (aluminum, copper, brass, nickel, zinc, titanium etc.) and plastics. We keep standard sheet sizes material on stock.
When placing orders it is of great importance that you specify the alloys for the individual materials.
The wide variety of ancillary operation options is the basis for the variety of final products. Examples of post-processing include drilling attachment holes or other additional holes, cutting, notching, bending, rolling, punching or circle cutting, profiling, welding, torch cutting and laser treatment. Product examples: Hardening and galvanizing baskets, transportation baskets and containers, shelving walls, modern outdoor and indoor fittings and fixtures.
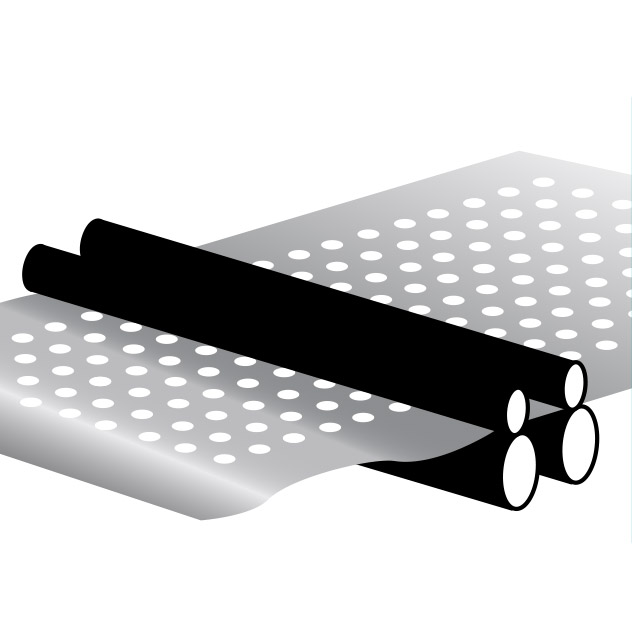
Leveling machines
All perforated sheets and coils will be leveled after perforating since strains are introduced into the sheet. The quality of leveling will depend on the material being used, its thickness, the nature of the margins and the details of the perforations themselves. The larger the margin and the closer the perforations, the more difficult it will be to level the perforated plates.
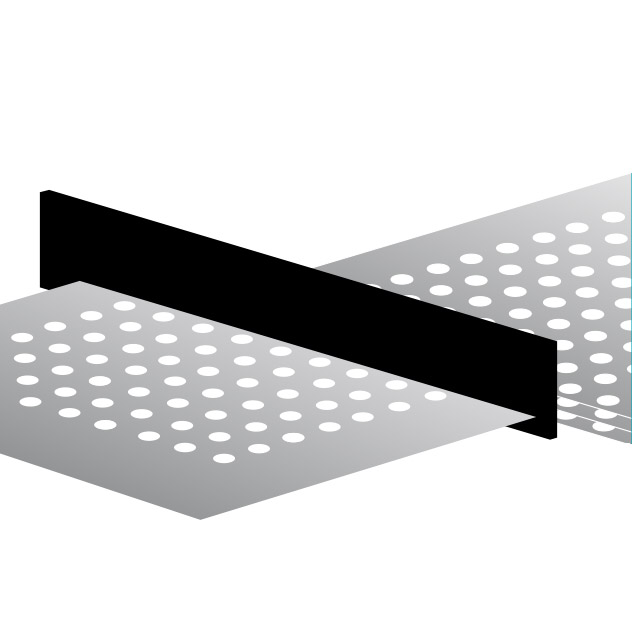
Guillotines
Here the panels are cut to the specified dimensions. The strip which is trimmed away should not be smaller than the thickness of the material.
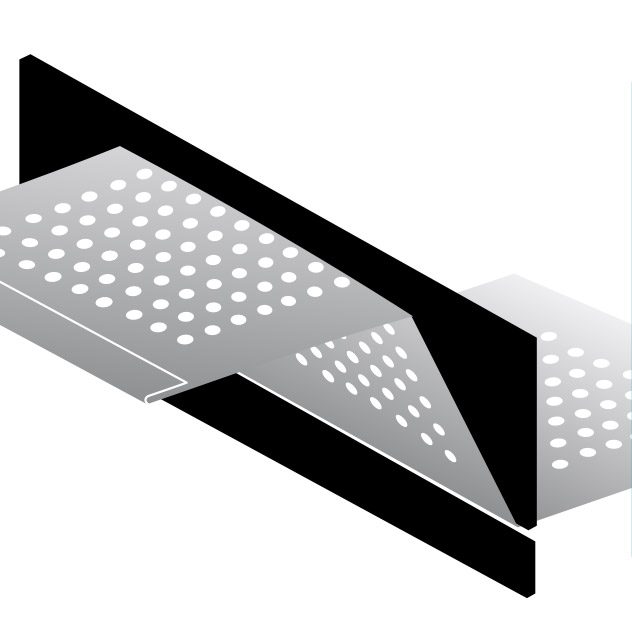
Press brake
The manufacturing process permits only rounded-edge designs. All the materials which are suitable for bending can be used here. It is assumed, however, that sheet products are used as the working material. Typical profile shapes includes angle irons, U, Z, C and top-hat profiles, and variations of the same with seamed edges.
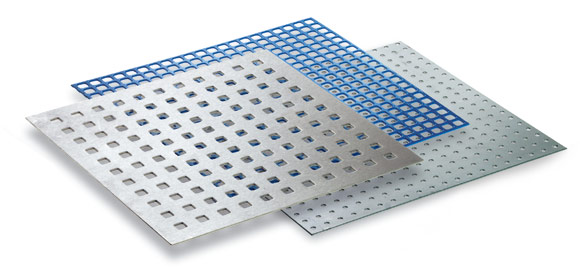
Polished or brushed surface
Perforated plates with a polished or brushed surface are used in applications where appearance is important. The plates can be polished or brushed either before or after punching.
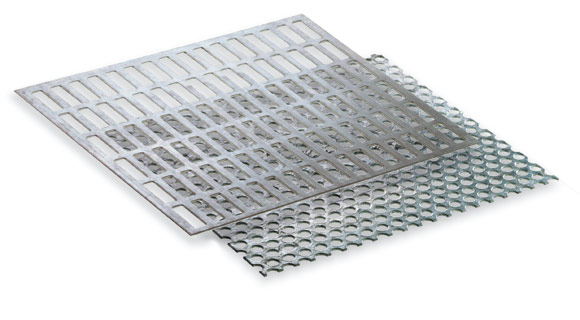
Lightly oiled, degreasing with an oil binder, machine degreasing
Unless otherwise specified, the perforated plates will be shipped with a fine film of oil, which can be felt and seen. Where an oil binder is spread and brushed away a relatively oil-free surface will be achieved but residues will remain in the holes. If the perforation plate is to be entirely free of lubricants it will have to be chemically degreased (machine degreasing). This method is suitable only for stainless steel materials and non ferrous metals.
Hot-dip galvanizing
The perforated plates will be dipped in molten zinc. Please note: The hole diameter should be > 5 mm, as the holes could easily be clogged at smaller diameters. Following galvanizing the perforated plates may exhibit a rough, grainy surface.
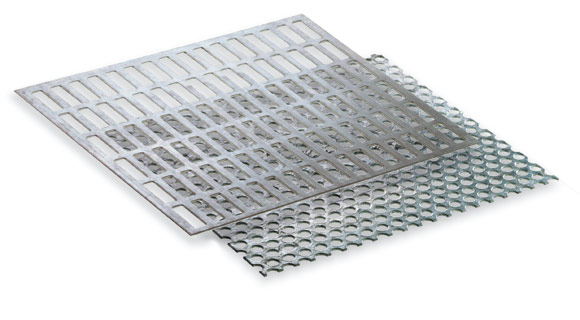
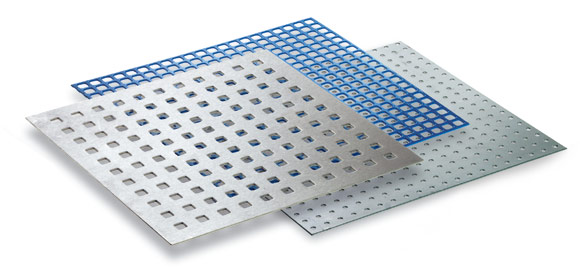
Plastic powder coating
Coating with a polyurethane lacquer or polyester powder not only lends an attractive appearance but at the same time provides very effective corrosion protection. When dealing with pre-galvanized material, plastic coating offers a very good alternate to hot-dip galvanizing after punching. We would request that you indicate in your order the use for which the plate is intended so that we can select in advance the most suitable finishing method.